24
2019-01
Attractivechina partners with PUNJAB STAINLESS STEEL INDUSTRIES to deliver Non-stick Cookware Coating Production Line
Author:
Chuangzhitz
At Punjab Stainless Steel Industries, they strive to lead in the invention, development and manufacture of the industry's most advanced Stainless Steel Cookware, Hollowware, Pressure Cooker, Restaurant ware, Kitchenware and all the Stainless Steel and Aluminum Items.
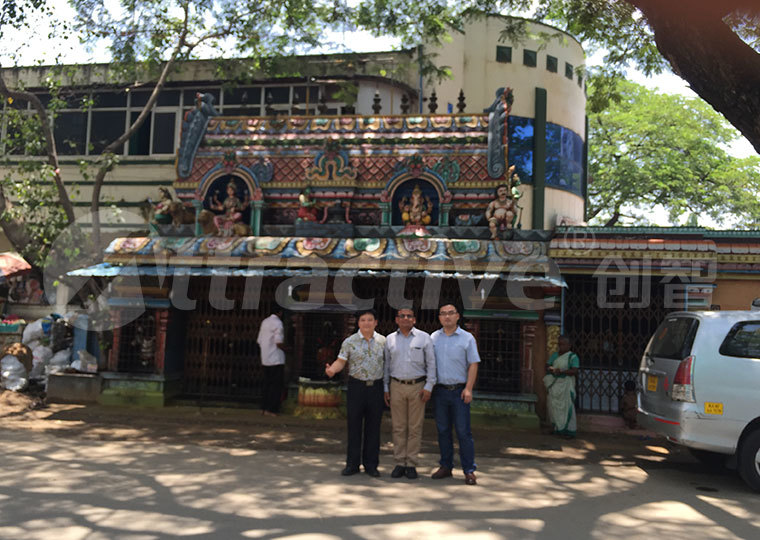
From its inception Since 1947, Punjab Stainless Steel Industries has been based on a set of fundamental values.
A benchmark for quality on the international market, Punjab Stainless Steel Industries has always anticipated the need to ensure ongoing improvement in quality standards, investing wherever necessary to exceed customer expectations and set the bar higher in the relevant market.
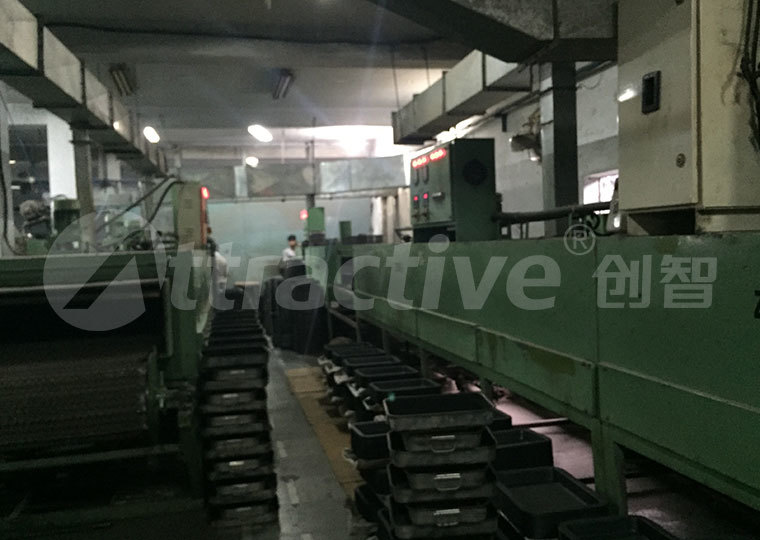
Attractivechina has been focusing on the field of customized automation production line for 30 years, which integrates r&d, production, sales and service. Attractivechina can design production line according to the actual situation of customer, and provide customers with satisfactory products and services. Recently supplied Punjab Stainless Steel Industries a Non-stick Cookware Coating Production Line to enhance productivity and enable increased flexibility in view of changing market trends and customer needs.
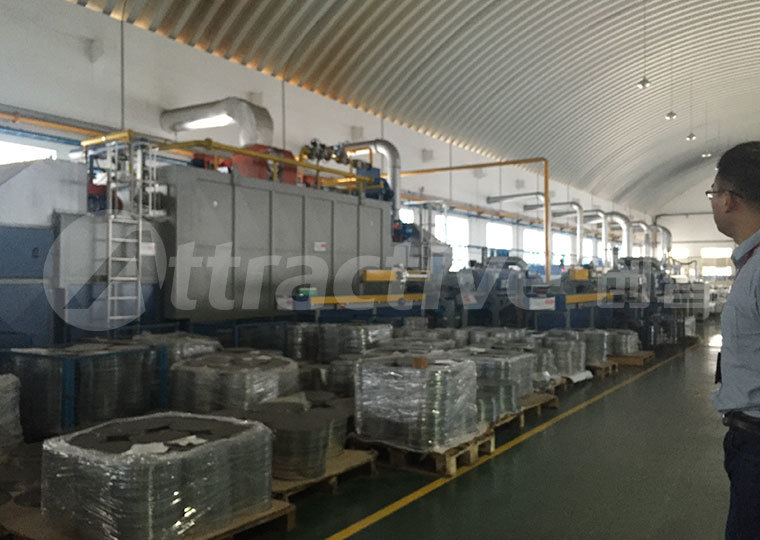
Technological Process:
A. Process Flow (aluminum pot washing)
Loading→Alkali washing→Washing→Neutralizing→Washing→Hot water washing→Blow water →Drying→Cooling→Unloading
B. Process Flow (stainless steel pot washing commonly use with aluminum washing line)
Loading→Degreasing→Washing→Washing→Hot water washing→Blow water→ Drying→Cooling→Unloading
C. Sandblasting Process Flow
Loading → Sandblasting → Unloading
D. Spraying Line Process
Loading → Automatic dedusting → Preheating → Spray primer →Transfer workpiece → Drying → Fast cooling→Transfer workpiece →Automatic dedusting → Preheating → Spray middle and top paint → Turn to high-temp.line → Low temp. Volatilization → Heating phase → High-temp. curing→ Strong cooling→ Unloading
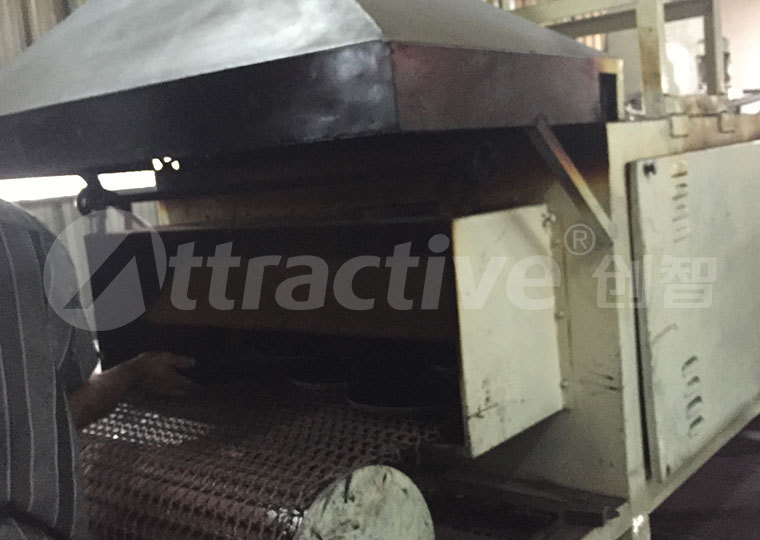
The benifits of the whole production line:
1.The spraying booth equipped with multi-stage sprinkler system to reduce 30% of the paint mist in the exhaust gas of the spray booth and also reduce the cleaning deposit cost;
2.Tracking spray has high speed reaction, fixed sprayi reduce the paint consumption, at amount can saving the 10% of the paint;
3.Using the waste heat of the high temperature furnace, through the hot chamber exchanger of the drying furnace, to achieve the effect of energy saving;
4.The three-stage design of the high-temperature furnace prevents the heat in the furnace from dissipating through the conveyor belt, and the transition mechanism ensures the smooth transportation and long-term operation stability;
5.Inner paint line and ceramic inner paint process can be quickly converted to save process time;
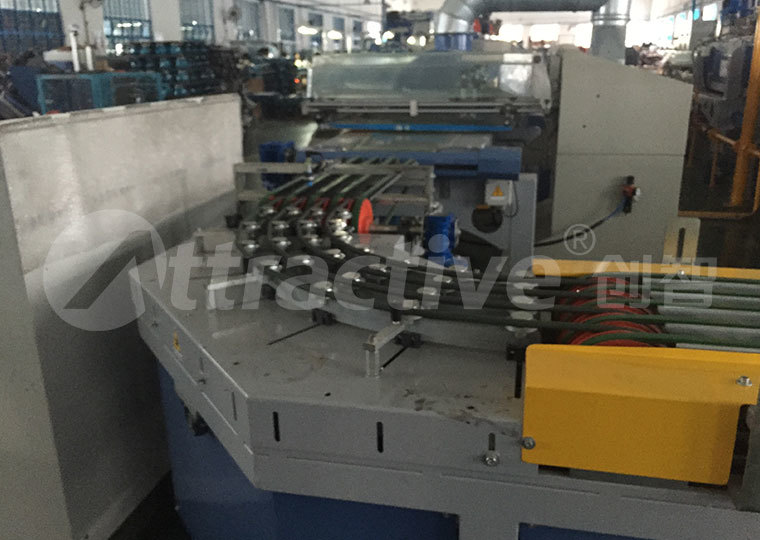
6.Whole line with less empty chain, reduce the number of fixtures;
7.The conveyor belt with heighten type, which is 60mm higher than the traditional chain, so as to strengthen the stability of the conveyor belt and reduce the workpiece shaking;
8.Outer spray line equipped with workpiece rotation device to make the workpiece rotation stable and uniform, ensure the painting quality and good appearance;
9.High temperature furnace exhaust adopts variable frequency power exhaust, reasonable distribution, at the same time to meet all kinds of coating and ceramic oil process requirements.
SEO: