Related News
03
2025
-
07
How to Effectively Reduce Downtime Losses in Painting Equipment?
Author:
Chuangzhi Coating
In today's highly competitive manufacturing environment, the continuous and stable operation of painting lines is crucial for a company's production efficiency and cost control. However, painting equipment inevitably encounters various faults during operation, leading to production line downtime and significant economic losses for enterprises. To effectively reduce downtime losses, companies need to shift from the traditional breakdown maintenance model to more efficient maintenance strategies, with predictive maintenance being a notable option.
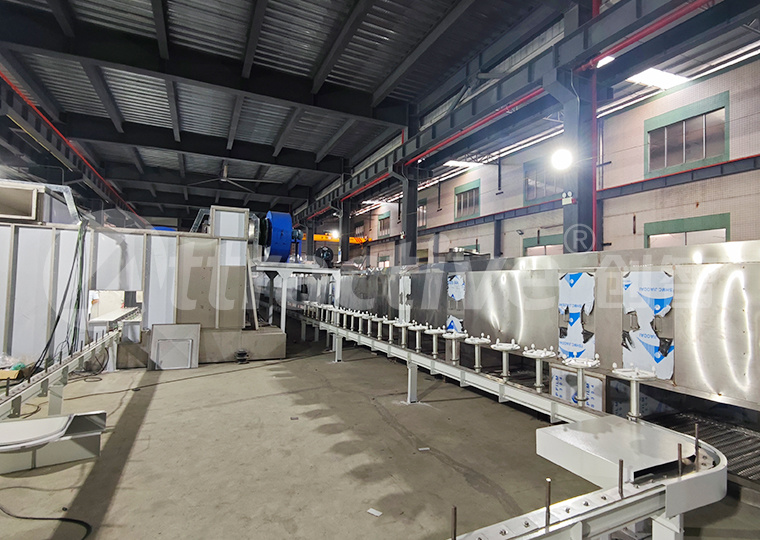
I. Limitations of Breakdown Maintenance Model
The traditional breakdown maintenance model, which involves repairing equipment after it fails, may seem straightforward, but it actually has many limitations. Firstly, after a fault occurs, companies often have to wait a considerable amount of time for maintenance personnel to arrive and diagnose the problem, extending downtime. Secondly, emergency repairs need to be completed within a limited timeframe, increasing repair difficulty and costs. Furthermore, the breakdown maintenance model does not prevent equipment failures, resulting in persistently high failure rates and posing continuous economic pressure and safety hazards to companies.
II. Advantages of Predictive Maintenance
Compared to breakdown maintenance, predictive maintenance offers significant advantages. Predictive maintenance monitors equipment operating conditions in real-time, collects and analyzes equipment data to predict the timing and causes of equipment failures. This allows companies to take preventive measures before equipment failures occur, avoiding or reducing downtime events. Additionally, predictive maintenance helps companies reasonably arrange maintenance plans, reduce maintenance costs, and improve equipment utilization.
As a painting line equipment manufacturer, we understand the importance of predictive maintenance. Therefore, we incorporate advanced sensor technology and data analysis algorithms into the equipment design and manufacturing process, enabling the equipment to self-monitor and issue early warnings. When the equipment exhibits abnormalities, the system immediately sends an alarm and provides detailed fault information and maintenance suggestions, helping companies quickly locate the problem and take corresponding measures.

III. Key Steps for Implementing Predictive Maintenance
Implementing predictive maintenance requires companies to take a series of key steps. Firstly, companies need to establish an equipment monitoring system to collect equipment data in real-time. Secondly, they should use data analysis tools to process and analyze the collected data, identifying early signs of equipment failures. Then, based on the analysis results, they should develop a maintenance plan and perform maintenance before equipment failures occur. Finally, they should evaluate and improve the effectiveness of predictive maintenance, continuously optimizing the maintenance strategy.
When implementing predictive maintenance, companies also need to pay attention to the following points: ensuring data accuracy and completeness; selecting appropriate data analysis tools and methods; and strengthening employee training to improve their understanding and operational skills of predictive maintenance.
IV. Conclusion
The transition from breakdown maintenance to predictive maintenance is an important way for companies to improve the operating efficiency of painting line equipment and reduce downtime losses. As a painting line equipment manufacturer, we will continue to focus on technological innovation and product development, providing companies with more efficient and intelligent maintenance solutions for painting equipment. By implementing predictive maintenance, companies can achieve precise prediction and effective prevention of equipment failures, ensuring the continuous and stable operation of painting lines and providing strong support for their sustainable development.